De Capitán Álvaro Macías Torrijos
La planificación y el desarrollo de la estrategia ofensiva de taponamiento en respuesta a una fuga de gas líquido es de suma importancia para mitigar los riesgos asociados a la inflamabilidad y la acumulación de gas. Esta fase consistió en priorizar el sellado de la fuga en fase líquida, que plantea mayores riesgos debido a su potencial para generar una cantidad significativa de gas. Podréis leer la primera parte de este artículo aquí.
Fase 3: Planificación y desarrollo de la estrategia ofensiva de taponamiento
Se priorizó el taponamiento de la fuga de gas en estado líquido para mitigar los riesgos de inflamabilidad y acumulación de gas en zonas bajas. La fuga en fase líquida es de mayor riesgo que en fase gaseosa, ya que emana a -20°C puesto que 1 litro de líquido es capaz de generar unos 250 litros de gas.
Simultáneamente se evaluaron las posibilidades de la extracción del gas del depósito. Se solicitó un equipo de técnicos de urgencia de Repsol-Butano cuyos conocimientos y actuación serían clave.
El almacenamiento de GLP en este tipo de depósitos tradicionalmente se realiza en recipientes cilíndricos horizontales construidos con acero al carbono de 3 mm de espesor. Suelen estar compuestos por dos fondos y una o varias virolas que, según el tamaño del depósito, están unidas por los correspondientes cordones de soldadura. La presión de diseño de los depósitos enterrados con capacidad superior a los 7 m3 puede alcanzar los 17 bar (Imagen 1).
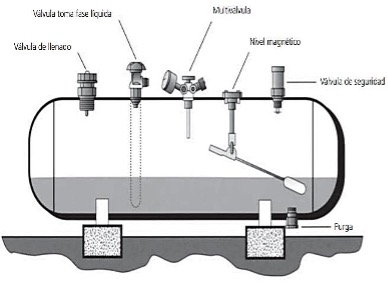
Todas las válvulas, presentaban un avanzado estado de corrosión por oxidación y algunas de ellas además había sido dañadas por el caso de la excavadora. Por tanto, se encontraban tan deterioradas que cualquier actuación sobre las mismas podría producir su rotura definitiva y provocar una fuga masiva de gas o de líquido. Sin embargo, la válvula de salida de fase gaseosa sí que parecía tener la suficiente resistencia estructural para poder acoplar en serie sobre ella otra válvula que si permitiera sellar la fuga.
Se descartó la posibilidad de realizar un trasvase del contenido por hallarse éstas inservibles, optándose por la quema controlada del gas y la siguiente estrategia:
- Introducir agua en el depósito a través de la válvula de la fase gaseosa, que al ser más denso que el propano líquido, se depositaría en el fondo, hasta rebasar la altura del tubo que sirve de salida de la fase líquida (Imagen 2). Con esta acción, en vez de fugar propano líquido, fugaría agua. La fuga de agua sería más fácil de controlar, además de no tener riesgo, ya que se congelaría en la salida produciendo un sello de hielo. Este auto taponamiento, aunque fuese parcial, produciría una reducción de la presión que permitiría la aplicación de una pasta tapa fugas (limitada su uso a 0,5 bar).
- Colocar en serie, en la salida de la fase gaseosa, un acople con dos salidas con sendas válvulas. Una de las salidas dispondría de un racord tipo Barcelona para introducir agua en el depósito, y la otra salida un sistema de rosca para conexión de una “T” con un manómetro y una toma roscada para acople de tubería flexible que serviría para la extracción del gas. El manómetro monitorizaría la presión del interior del depósito. Por la configuración del sistema es imposible realizar la extracción del gas y simultáneamente introducir agua.
- Mitigada la fuga, se procedería a montar una instalación de quemadores de gas.
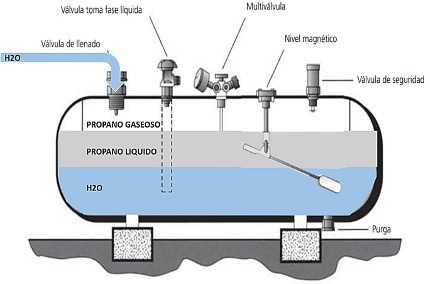
A partir de este momento se planificó el siguiente plan de acción en dos fases:
- 1ª Fase: Mejorar las condiciones de seguridad para facilitar el resto de los trabajos.
– Instalar una red de monitorización de gases.
– Protección personal de intervinientes: traje de protección criogénico.
– Instalar una válvula en el depósito para mitigar la fuga en fase líquida.
- 2ª Fase: Vaciado del depósito e inertización.
– Extracción del gas y quema controlada en zona segura.
– Llenado del depósito con agua para inertización.
– Monitorización constante de gases y productos de combustión.
Monitorización de gases
Hasta ese momento se estaban empleando los detectores de gases Multi Rae Lite equipado con 6 sensores, entre los cuales había uno de perla catalítica que mide la inflamabilidad.
Esta red permitía distribuir detectores en diferentes lugares que estaban conectados a un receptor inalámbrico. Con ello se pudo realizar un control constante de los valores y vigilancia de alarmas. El equipo receptor Echo View Host (Imagen 3) ofrece la posibilidad de gestionar las señales y lecturas en tiempo real.
En la zona de trabajo y de forma periódica en el entorno se dispuso de los detectores de gases modelo Micro Rae para monitorizar el riesgo de inflamabilidad.
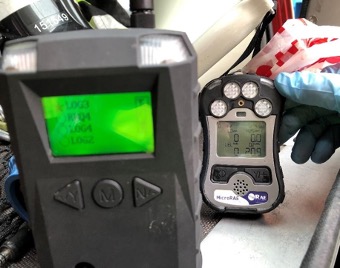
Respecto al nivel de protección personal, se determinó que, para hacer frente a los riesgos de mayor peligrosidad, iba a ser necesario trabajar con trajes de protección criogénica. Estos trajes están construidos y diseñados para soportar temperaturas de varias decenas bajo cero, y habría que vestirlos sobre el equipo E2 con protección respiratoria.
En su parte superior, estos depósitos disponían de una serie de orificios y tubuladuras para el alojamiento de las válvulas y componentes de medición (manómetro e indicador de nivel) necesarios para su utilización. En la parte inferior tenían unos soportes, así como unas orejetas en la parte superior para facilitar su traslado, descarga y emplazamiento.
Instalación de adaptador y sistemas de válvulas sobre válvula de salida de fase gas
El riesgo que podría tener realizar una acción no adecuada en el proceso de instalación del adaptador obligaba a que los equipos que lo iban a realizar debían actuar sin improvisación.
Esta operación se complicaba aún más por los equipos de protección que tenían que llevar los intervinientes.
Este estudio previo fue posible realizarlo gracias a que el equipo de técnicos de Repsol puso a disposición de bomberos un juego de válvulas y llaves idénticas a las que se instalan en el depósito. Los equipos pudieron identificar las diferentes válvulas y practicar la maniobra previamente.
Durante todo el proceso también se protegió la zona con líneas de agua con mangueras de tipo reforzado (se emplean para trabajar en presiones superiores a 20 bar; Imagen 4). La presión en el depósito podría ser hasta 17 bar, por tanto, habría de inyectar el agua en el interior a presión superior a la que pudiera ejercer el gas. En el caso que el depósito tuviera una presión inferior al máximo de 17 bar, la presión podría aumentar en el proceso de inyección de agua. Esto es debido a que el agua aporta calor al gas licuado favoreciendo su evaporación y, por tanto, aumentando la presión en el interior del depósito.
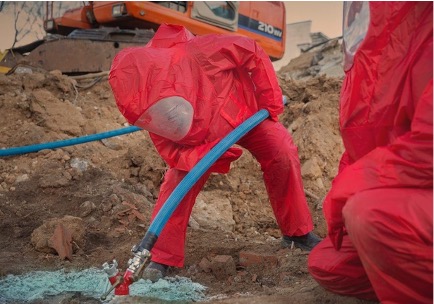
Una vez instalado con éxito el acople con sus válvulas y el manómetro, éste indicaba una presión de 3,4 bar. Se inyectó agua hasta que cesó la fuga de propano líquido y se aplicó pasta tapa fugas.
Esta fase de la intervención finalizó sobre las 21 horas del día 10 de enero. Actuaron un total de 12 dotaciones de bomberos, 2 patrullas de Policía Municipal y una ambulancia.
Fase 4: Extracción de gas y quema controlada
En la mañana del día 11 de enero se desplazaron dos coches de mandos con el Jefe de Guardia y tres asesores de la Unidad NRBQ de Bomberos. En la inspección visual se observó que se había producido un tapón de hielo durante la noche. No obstante, se continuó con la monitorización sin obtener valores de alarma.
También se revisaron y monitorizaron las viviendas sótanos y sumideros, siendo todos los valores normales, sin presencia de gas propano.
Para la quema controlada del gas, los técnicos instalaron un tubo flexible de gas con dos quemadores en su extremo final. Para elegir la zona de se tuvo en consideración lo siguiente:
- Zona elevada respecto a la fuga. El propano es más pesado que el aire, por tanto, se eliminaba el riesgo de hacer la quema en una zona con riesgo de acumulación de gas.
- Alejado y al barlovento de la zona de fuga. Se monitorizó de forma constante la dirección del viento para evitar que gas de la fuga pudiera ser arrastrado por el viento a la zona de los quemadores.
- Zona alejada de las viviendas para evitar alarma y riesgo de arrastre de gases producto de la combustión.
Los técnicos de Repsol-Butano instalaron un medidor de volumen de fase líquida acoplado al sistema de nivel magnético, que permitió estimar que había unos 725 kg de propano.
Una vez realizada la instalación de los quemadores, antes de iniciar la quema controlada del gas, se procedió a:
- Verificar la estanqueidad del quemador, control de la red de monitorización de gas y recorrido perimetral.
- Desplegar dos líneas de mangueras conectadas a un acortinador que protege el edificio más próximo y al quemador y una línea de 45 mm con surtidor.
- Efectuar comprobaciones cada 30 minutos para verificar el descenso del nivel y vigilar la presión.
- Informar a los vecinos y resto de ciudadanos.
- Realizar el encendido manual del quemando.
Mediante el control de la presión y del nivel magnético se podía controlar la cantidad de gas restante que quedaba en el interior. Se previó que cuando el flujo del gas comenzase a disminuir, se detendrían los quemadores para introducir agua, gasificar el propano licuado y volver a conectar la instalación del quemador. Esta operación se repetiría sucesivamente hasta agotar por completo el gas y llenar de agua todo el depósito de combustible. La alimentación con agua iniciaría cuando la presión cayese hasta los 0,3 bar, presión a la cual el funcionamiento de los quemadores es inadecuado.
En la mañana del 12 de enero la presión descendió hasta los 0,3 bar, se cambió a un manómetro de menor escala y se empezó a de alternar el llenado con la quema.
Se dio por finalizada la emergencia sobre las 22 horas del 12 enero, habiendo sido activados entre ambos días un total de 38 dotaciones del Cuerpo de Bomberos del Ayuntamiento de Madrid.
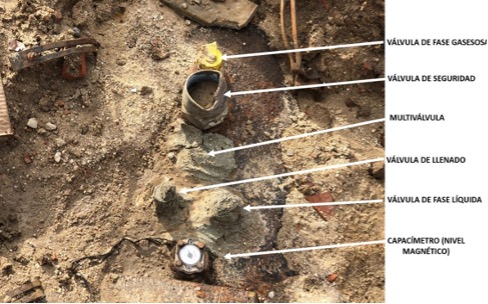
Para terminar, hay que destacar la labor que realizaron los técnicos de Repsol-Butano quienes demostraron unos amplísimos conocimientos técnicos y gran profesionalidad. Permanecieron en el lugar del siniestro durante todo el tiempo que duró la emergencia. Durante los trabajos conjuntos, dieron explicaciones tuvieron una gran capacidad didáctica y de trabajo en equipo. Esto favoreció un excelente clima de cooperación y, sin duda alguna, la resolución de un incidente extremadamente complejo.
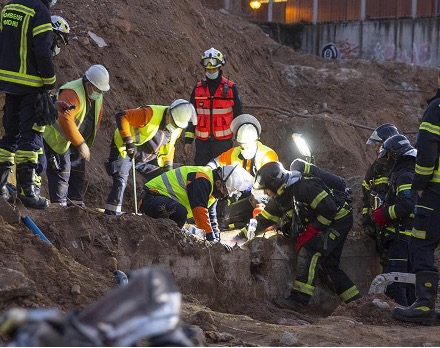
Conclusiones
Una vez finalizada la intervención, se analizaron las distintas fases y se obtuvieron las siguientes conclusiones:
- La monitorización de gases continua e ininterrumpida mediante una red de detectores permitió controlar los riesgos de inflamación o intoxicación de manera remota y centralizando los datos.
- El análisis de la interacción de varios riesgos, como el de inflamabilidad y riesgos térmicos por exposición a gas licuado a muy bajas temperaturas, permitió determinar unos niveles de protección personal adecuados.
- El apoyo de personal y recursos especializados de la Unidad NRBQ en tareas de asesoramiento técnico y logístico, reforzó la estrategia de intervención y permitió que los distintos relevos de personal dieran una continuidad en los objetivos planteados.
El Capitán Macías Torrijos es un apasionado del servicio público y está comprometido con su labor como bombero. Con más de 15 años de experiencia en el Cuerpo de Bomberos del Ayuntamiento de Madrid, de los cuales los últimos 6 ha desempeñado diversas funciones de responsabilidad y gestión. Ha sido Jefe de zona al cargo de 3 de las 13 estaciones de Bomberos, Jefe de unidad NRBQ y jefe de guardia en el parque central. Además, ha sido coordinador del grupo táctico “NRBQ-OTAN” durante la cumbre de la OTAN. Su experiencia incluye también la dirección del grupo especial de operaciones de descontaminación durante la crisis del COVID-19. Posee una formación académica y específica en respuesta a emergencias y se dedica a compartir sus conocimientos a través de la instrucción.