By Lt. Col. Christian Resch, Research and Development Manager, Federal Ministry of Defence Austria
Military interventions such as Cyprus (UNFICYP mission), the Golan Heights (UNDOF mission), the KFOR mission or disaster relief missions such as Italy, Armenia, Iran, or Sri Lanka, as well as the 2014 Ebola crisis and the current COVID-19 pandemic, have shown that there is a major need for non-destructive and environmentally friendly decontamination methods.
Current globalization trends and our interconnected world are creating a certain demand for CBRN protection. There is a lack of ability in the transportation of contaminated or infected soldiers or civilians (volunteers, embassy staff, etc.). Protection systems currently consist of impermeable systems. For example, mostly transparent “Snow White coffins” are used for transportation. These usually consist of a barrier film with rubber gloves in order to work on the patient. Elaborate filter units are needed to supply the patient with oxygen and at the same time to protect the outside world from the patient’s contamination – every contact or exchange is minimized.
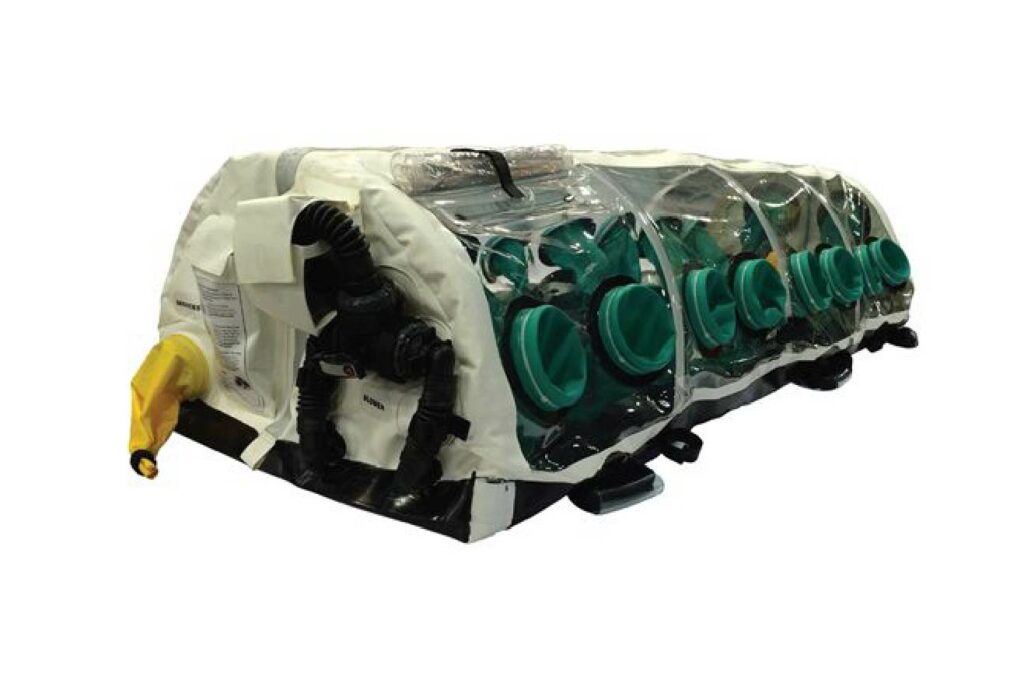
However, these systems must also be manageable, e.g., in aircraft. Closed systems create the challenge with decompression that they simply explode when the pressure drops in the cabin. In 2014, for example, planes from the US company Phoenix Air were used to fly highly infectious patients to Germany. Current solutions for CBRN air transportation are mostly based on a complete insulation unit, a separate exhaust air system and air conditioning (impermeable solution). Onboard, doctors and/or paramedics in protective clothing accompany the affected people in order to be able to guarantee appropriate medical care or qualified patient observation. The equipment of the isolation cells depends on the condition of the contaminated or sick person and on the type of contamination or illness. These solutions are on the one hand very cost-intensive and, on the other, only flexible to a limited extent and create a certain demand in decontamination.
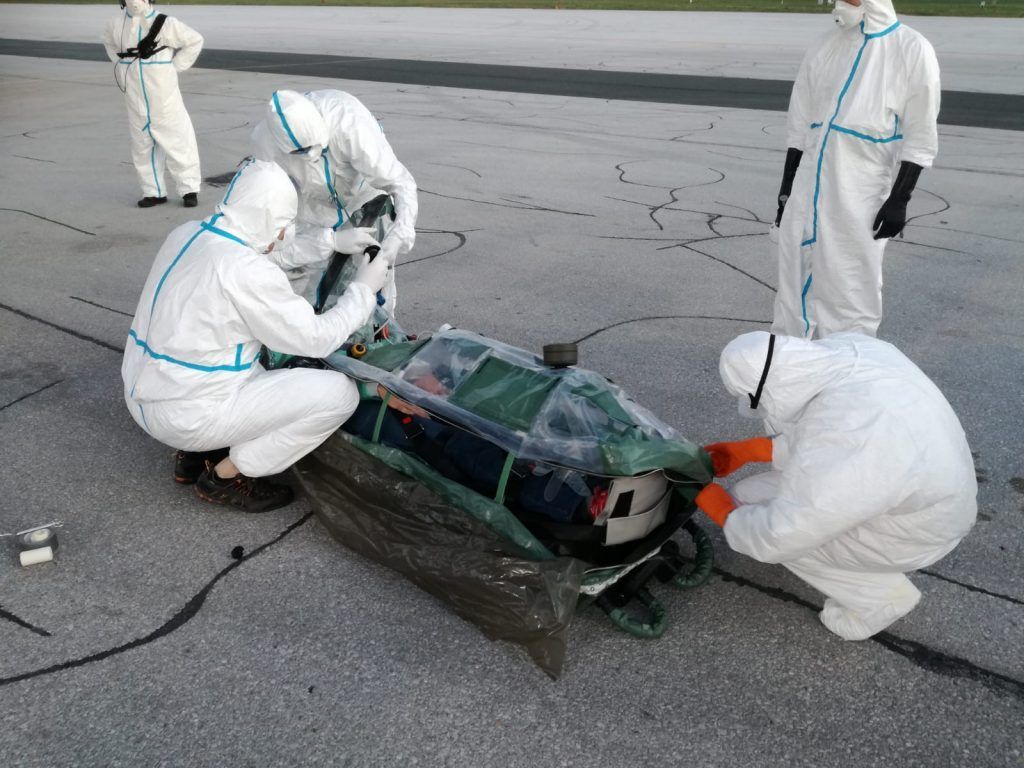
COVID-19 as a Driver for New Solutions in Decontamination
SARS-CoV-2, the causative agent of the infectious disease, is mainly transmitted via respiratory droplets and aerosols. Direct contact with virus-contaminated surfaces such as cell phones, computer keyboards, or door handles can also lead to infections, and even fecal oral transmission has been reported. The survival time of SARS-CoV-2 on various surfaces has been described by Riddell et al., who recovered infectious virus for time periods of up to 28 days when dried on non-porous surfaces like glass or metal at 20°C and 50% relative humidity. Another study recovered SARS-CoV-2 from plastic surfaces for up to 28 days at room temperature and 40-50% relative humidity. Even on the outer layer of surgical masks infectious viruses could be recovered after 7 days.
The single-use of personal protective equipment and specific demands in the transportation of contaminated patients create a great demand, which resulted in critical delivery delays for weeks and even months. On the other hand, the extensive use of face masks and other protective items led to a new form of massive waste generation. The disposal of huge amounts of used PPE components is an organizational challenge and a previously underestimated hazard for the environment. Due to the high stability and rapid transmission of the virus, the shortage of PPE, and the environmental pollution, an easy-to-use and sustainable decontamination method is needed to make an important contribution to combating the pandemic and protecting the environment through the safe recycling of PPE. Ultraviolet irradiation, vaporized hydrogen peroxide, moist heat, microwave-generated steam processing, and liquid chemicals were reported to sterilize PPE, but each method has its disadvantages – especially for aircraft equipment the demand is high. Any kind of filter consists of a combination of various materials, each of which is differently sensitive to chemical or radiation treatments. For example, liquid treatments such as alcohols require drying time, may cause oxidation, e.g., at metal clamps, and lead to a loss of filtering performance. Some materials are sensitive to heat or chemicals, and UV light is not suitable for materials with complex structures because areas shaded from the UV light will not be disinfected. Some masks also include electrostatically charged filter materials that may be adversely affected or even discharged by various treatments.
An alternative is the use of strongly oxidizing gas ozone. Ozone is naturally produced in the stratosphere by a two-step reactive process that forms ozone from oxygen and ultraviolet sunlight. It is well known as a constituent of the upper atmosphere, protecting organisms from the harmful effects of ultraviolet light. Less known is its industrial large-scale production for water purification, paper and pulp processing, disinfection of plant and animal products as well as the sterilization of medical supplies. It reacts with most elements of the periodic system except for noble metals, fluorine, and inert gases. The antimicrobial activity of ozone has been reported for a broad range of targets in bacteria on surfaces like glass, plastic, or steel. Its antiviral activity has been demonstrated for targets in enveloped and non-enveloped viruses, including the viral capsid, specific viral attachment epitopes, and viral DNA/RNA.
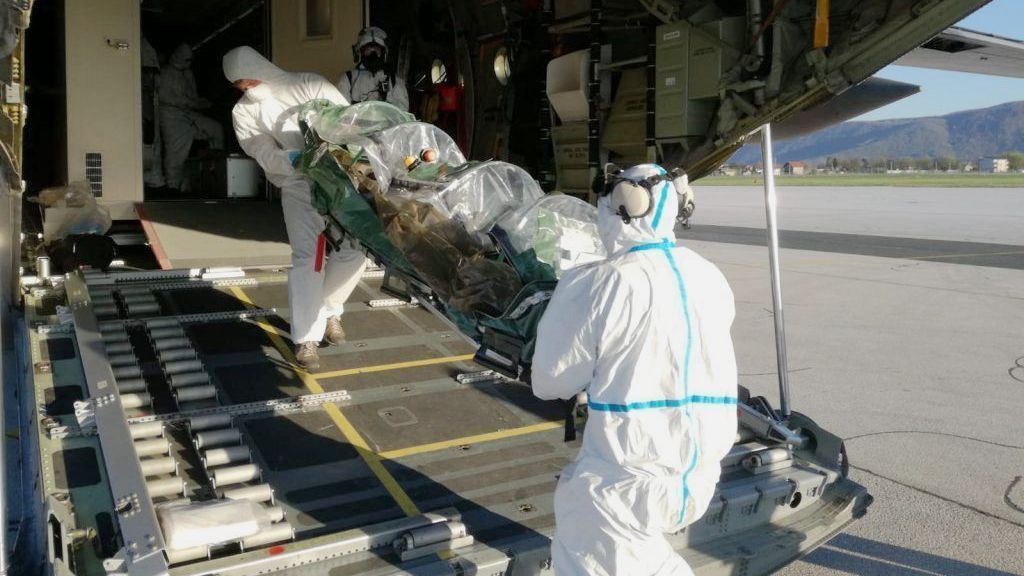
Cold Plasma Technology
Ozone decontamination of artificially SARS-CoV-2 has been reported recently. Since ozone dosages for decontamination of different surfaces vary a process is needed that is suitable for hard materials as well as PPE. A cold plasma generator enables the ionization of the surrounding gas at atmospheric pressure and ambient temperature. The generator provides a high ionization rate and an efficient ozone generation rate. Advantages are the low energy consumption during the ignition of the cold plasma in the air at atmospheric pressure, the low thermal load for materials (below 50°C), and the compact dimensions. Cold plasma applications have increased in a variety of different fields over the last decades, such as the automotive industry, medical devices, biomedical applications, skincare, and surface treatments. A relatively new application of cold plasma is the field of virus inactivation research. In contrast to other decontaminants, ozone can be produced fast and cost-effectively, and its environmentally friendly breakdown product oxygen does not leave harmful residues. The disinfection with ozone could help to overcome delivery difficulties of personal protective equipment by enabling safe reuse with further applications thereby reducing waste generation allowing regular disinfection of personal items with non-porous surfaces.
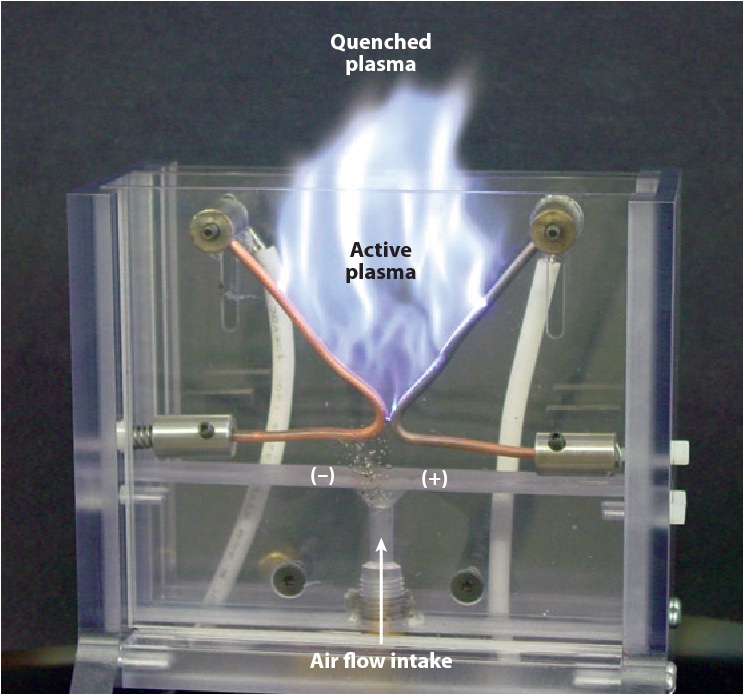
About the Author
Lt. Col. Christian Resch is a CBRN Defense Officer and working as Research and Development Manager in the Austrian Federal Ministry of Defense. In the Science, Research and Development Division he is responsible for all activities related to CBRN and C-IED. He has been working for over ten years in operational service of the Austrian Armed Forces. Lt. Col. Resch holds a Master’s degree in military leadership and in process and plant safety, where he is currently finishing his PhD on critical chemical infrastructures. He is also Managing Director of DCNA (Disaster Competence Network Austria), a science and research cluster in the field of security and disaster research.