How to evaluate the efficiency of a decontamination process in military operations
By Dr. Nikolaus Schneider, Head of the CBRN Decontamination Branch at Bundeswehr Research Institute for Protective Technologies and CBRN Protection (WIS)
“How clean is clean “or “Is clean, clean enough“ these questions are crucial for everyone who holds responsibility for a decontamination process. They imply the demand for procedures or technical solutions to reliably assess the success of a decontamination. A system for monitoring the decontamination and defining the remaining risks and hazards is required in order to guarantee the safe further handling of decontaminated material.
Decontamination Levels
Active decontamination operations reduce hazard levels by removing or neutralizing liquid or solid contamination. For military operations, NATO defines three levels of decontamination: immediate, operational and thorough. Immediate decontamination is carried out by individuals right after becoming contaminated. Whereas operational decontamination is carried out by an individual and/or a unit and is restricted to specific parts of operationally essential equipment or materiel in order to minimize contact and transfer hazards and to sustain operations.
Thorough decontamination is the level of decontamination where risk assessment becomes essential. Thorough decontamination is conducted by a unit to reduce contamination on personnel, equipment, materiel and/or working areas to the lowest possible levels, to permit the partial or total removal of individual protective equipment and to maintain operations with minimum degradation. NATO Standards like AEP-58 or AEP-7 define residual limits for different agents that have to be achieved by thorough decontamination.
A fourth level, clearance decontamination, is defined as “decontamination of materiel to a standard sufficient to allow unrestricted transportation, maintenance, employment or disposal” (STANREC 4784, currently under ratification). It is a post-conflict measure and not part of a military operation. There are no current agreed standards or levels for clearance decontamination of Chemical Agents. Available guidelines for “negligible risk” are up to a factor of 10³ below thorough decontamination. Clearance decontamination will not be considered in this article.
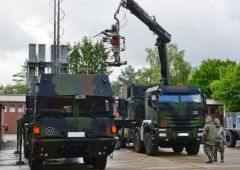
In the Field
From a military point of view, the direct and visual proof of the decontamination performance with field applicable equipment is desirable in order to have a quick hazard/risk assessment in action. This is quite simple for radiological measurements and, realistically seen, impossible in case of biological agents. For chemical contamination, it is not a simple yes or no question but requires differing approaches.
Colorimetric rapid tests, available as ready-to-use test sticks or sprayable liquids, could be suitable, at least with restrictions, as they allow only semi-quantitative assessment of the decontamination. They are capable of indicating residual traces of toxic substances on decontaminated surfaces, even in small quantities. However, they show cross-sensitivity to many decontamination agents (like the German GDS 2000), and it cannot be guaranteed that the NATO limit values for thorough decontamination will be displayed under all conditions.
Application tests have shown that these colorimetric test systems work pretty well for contamination pre-control to determine the degree and location of contamination on the surface, which may impact the decontamination measures to be carried out. However, after decontamination, they may well serve for risk estimation, but not as validated decontamination control.
Portable detection devices available on the market allow greater accuracy and quantifiability. The most suitable detection devices are based on flame ionization like Proengin AP4C, especially when specific sampler systems are used to improve sensitivity. The detection limit is sufficiently low, and reliable results are provided at least on contaminated but otherwise clean test surfaces. On real surfaces, interferences with dirt, oil, lubricants and particularly residual decontaminants occur and the results are ambiguous and not clearly determinable.
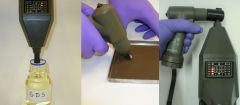
However, even if an equipment is available to detect down to the given thresholds for thorough decontamination under all conditions, this would give only evidence for a very limited part of the surface of a vehicle. It will be nearly impossible to detect all relevant points that might still pose a hazard after decontamination. The pictures below from decontamination testing of an IFV PUMA with some detailed views illustrate clearly the problem of decontaminating the complex surfaces of modern battle tanks and evaluating the efficiency of decontamination.
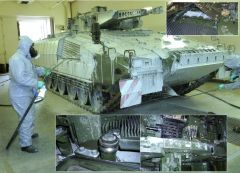
Although risk assessment after military decontamination operations is an important requirement, a general solution for decontamination control cannot be given yet. “Easy” solutions are not available at short notice and realistic goals need to be defined.
In the Laboratory
Laboratory-based methods are much more sensitive and do provide clear and assured results about the efficiency of a decontamination process but are not applicable for field use and require sampling. Most customary sampling procedure would be taking swabs, albeit far from being reproducible. For volatile compounds, gas samplers could be considered under defined conditions. Laboratory methods are well established to define contact and inhalation hazard during testing and evaluation of decontaminants, decontamination methods and procedures. If the efficiency of a decontamination process is validated to securely confirm the criteria for thorough decontamination, the process is carried out under fully reproducible conditions and it can be verified that all surfaces are in contact with a sufficient amount of decontaminant, the safety of a certain decontamination process can be declared.
Validated Decontamination Process
This brings us to the third option for decontamination control, the process-based approach. For manually operated decontamination systems, a better visibility of the decontaminant on the surface would be the first step to improve the reliability of decontamination in the field. GDS 2000 for example, a decontaminant in service in German Armed Forces, is a clear, viscous liquid. Dyeing the decontaminant before application with colored or, even better, fluorescent substances will significantly improve the manual decontamination processes by allowing a better control of fully covering the surface with the decontaminant. The picture shows a vehicle with a fluorescent GDS 2000 mixture.
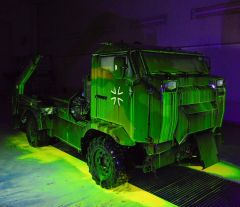
Future decontamination systems will certainly evolve to fully or partly automated, intelligent devices with advanced technologies to improve process safety. The success of the decontamination will be ensured through prior validation of the overall process, and a precisely defined decontamination carried out under similar process parameters. A defined, automated process without the “human” error factor will be the key to safe decontamination.
A concept study for the automation of decontamination processes has been successfully completed in cooperation with industry. After a technology survey, two major concepts were considered in depth, both having advantages and disadvantages. One solution is based on movable robot arms, which allow very reproducible procedures and decontamination results, but will be technically complex and correspondingly expensive. Another option are foldable, transportable portal solutions, functionally comparable to car washing systems, combined with a contour recognition or a database with validated working conditions for optimal decontamination for every type of vehicle or equipment. Weighing the pros and cons according to this study, a portal systems option would be technically easier to develop and to realize, less expensive and more reliable. Even so, both concepts are still viable options and will be considered further on. A small-scale demonstrator with a collaborative robot arm is currently under development.
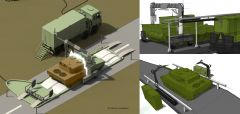
Conclusion
Although risk assessment after military decontamination operations is an important requirement, a general solution for decontamination control cannot be given yet. “Easy” solutions are not available at short notice and realistic goals need to be defined.
An overall approach should be based on three pillars.
– Field applicable systems and procedures: Several options were considered and tested, all having different capabilities and limitations. They may serve for risk estimation but are not applicable for comprehensive decontamination control.
– Validated laboratory analyses: The preferential field of application will be test and certification of decontaminants or decontamination processes by determining the residual contact and inhalation risks in models and small-scale tests.
– Process-based approaches: This will range from the improvement of current manual procedures to fully automated systems in the future.
Still, a lot of work remains to be done.
About the Author
Dr. Nikolaus Schneider has studied chemistry at the University of Saarland, Saarbrücken and earned his PhD with a thesis on the separation of radioactive Cesium from nuclear waste. He is the Head of the CBRN Decontamination Branch at Bundeswehr Research Institute for Protective Technologies and CBRN Protection (WIS) in Munster, Germany. He started his career at WIS as expert for radiological/nuclear decontamination but soon widened his fields of work to the development and testing of decontamination equipment with regard to C-, B- and RN Decontamination. He is long-term member and Secretary of the Hazard Management Panel under the NATO Joint CBRN Defence Capability Development Group.
All photos © WIS, except “Concepts for Automated Decon Systems” © by Kärcher Futuretech.
Article cover photo ©Flickr